関連ブログ
設備能力を測る指標の一つにサイクルタイムがあります。
サイクルタイムはある工程がその作業を終えるのに何秒かかるか?を測るものです。
その単位は【秒/個】で表されます。
定義はシンプルですが、ある工程のサイクルタイムを算出しようとしたときに
2つの方法があることはご存知でしょうか。
2つの方法は意味合いが全く異なりますので注意が必要です。
さてここで 全自動組立ラインの中の一つ、ねじ締め工程を考えてみます。
前工程で組立を行い、カバーが被さった状態で搬送用パレットに乗ったワークが
ねじ締工程にチェーンコンベアで送られてきます。
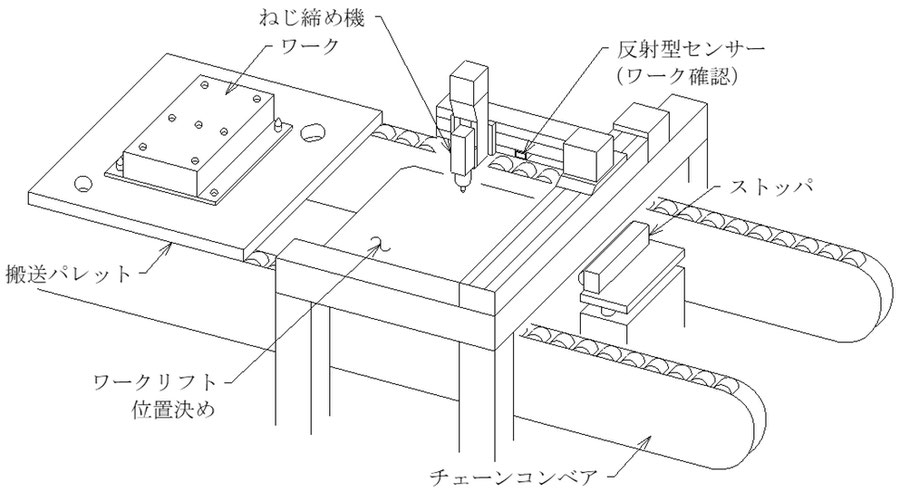
作業フロー
①前工程からワークが流れてくる。(センサー検知)
②ワークをリフトアップしてコンベアから縁切りするとともにピンで位置決めをする。
③ねじ締め機によるねじ締め作業
④作業が終わったら、リフトダウンしてワークを開放する。
⑤ワークは後工程へ流れる。
繰り返す。
①~⑤の流れをタイムチャートで示します。
ワークが到達して作業を行い、完了後にワークを後工程へと流す、
そして次のワークが到達するまでを1サイクルとします。(①→①)
これを工程サイクルタイムと呼びます
一方、機械が行う作業に絞ったサイクルタイムを見る場合があります。
これを機械サイクルタイムと呼びます。
機械サイクルタイムには
純粋に作業のみを見る機械サイクルタイム1(②→④)
ワークのセット(この場合リフトアップ・ダウン)を含めた機械サイクルタイム2(①→④)
この2種類の見方があります。
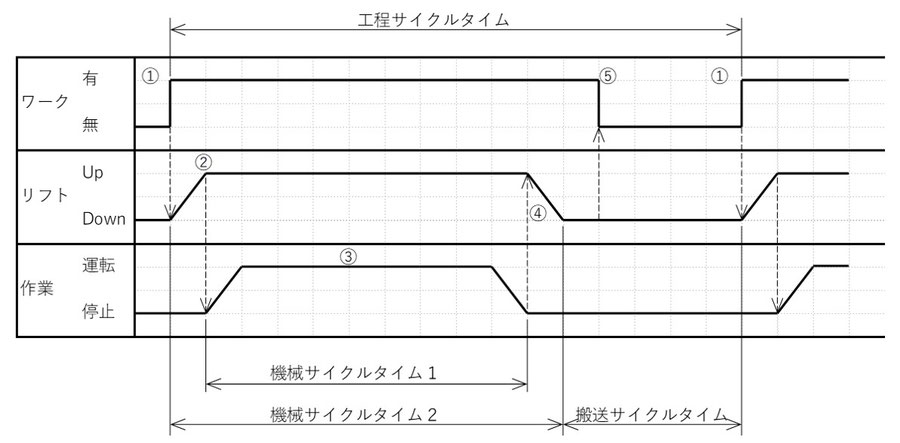
通常サイクルタイムと言えば、工程サイクルタイムを指します。
例えばライン構想を練るときに次のような計算をします。
・1日当たりの生産量が12,000個
・1日当たりの生産時間が10時間だから、、、
・1時間当たり1,200個、1分当たり20個、、、
・つまりタクトタイムは3秒/個だな。
・と言う事は各工程のサイクルタイムは3秒/個以内にする必要があるな。
*タクトタイム=ある製造ラインを経て完成品が出てくるピッチ(時間)のこと。
この場合のサイクルタイムは工程サイクルタイムを指します。
サイクルタイムを解説している書籍やブログなどはたくさんありますが、
そのどれもがほぼサイクルタイム=工程サイクルタイムの説明になっています。
設計段階での検討は工程サイクルタイムを見るべきです。
しかし、ラインを稼働させ運用する段階では不都合が出てきます。
設備に問題がなくとも④→①の時間、搬送サイクルタイムにバラツキが出るからです。
バラつきの原因は
・前後工程とのサイクルタイムのアンバランス
(最もサイクルタイムが遅い工程をボトルネック工程という)
・段取り替え
・チョコ停やドカ停などの設備トラブル
などがあります。
実際の工程サイクルタイムを測定するとこれらの停止時間が含まれてきます。
この結果サイクルタイムが遅かったからといって設備改善をしても
的外れな改善になる可能性があります。
なぜなら他責原因で設備が動いていない可能性があるからです。
段取り替えが複雑で多くの時間をとられている工程のサイクルタイムが長くなっているときに
設備改善をしても効果は薄いのです。
この場合、サイクルタイムを細かく評価すると搬送サイクルタイムにバラツキが出てきます。
搬送サイクルタイムのバラつき要因、段取り替えや待機時間などを押さえて
改善を行うと高い効果を得ることができます。
コメントをお書きください
西田 宏 (金曜日, 10 1月 2020 12:23)
3分程でのスポット情報がほどよく頭の刺激となり参考になりました。今後のレポートの楽しみにします。