◆自動機の設計では位置決めが悪いと失敗します!
◆はじめに
本記事は【位置決めその1】の続編です。
◆位置決め、3つの設計
その1にも書きましたが、位置決めの考え方には図1に示すように、大きく分けて3つあります。
1.基準となるブロックの面に押し当てて位置を決める方法 (位置決め要素その1)
2.V溝に丸物をあてて中心の位置を決める方法 (今回)
3.位置決めピンを使って位置を決める方法 (位置決め要素その3)
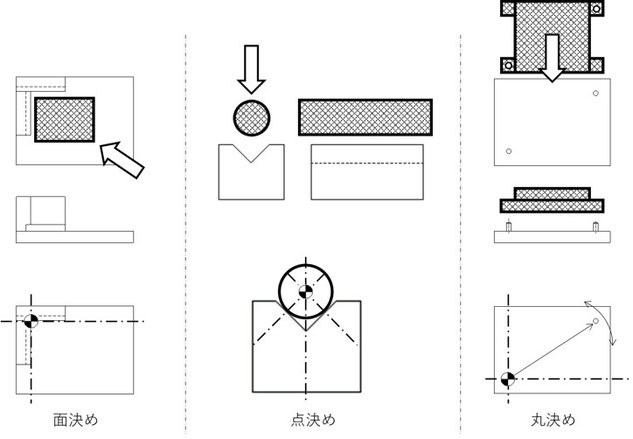
2.V溝に丸物をあてて中心の位置を決める方法
代表的な円筒物の位置決めにはVブロックがあります。Vブロックはさまざまなサイズが市販されており手軽に扱えるため広く使用されています。
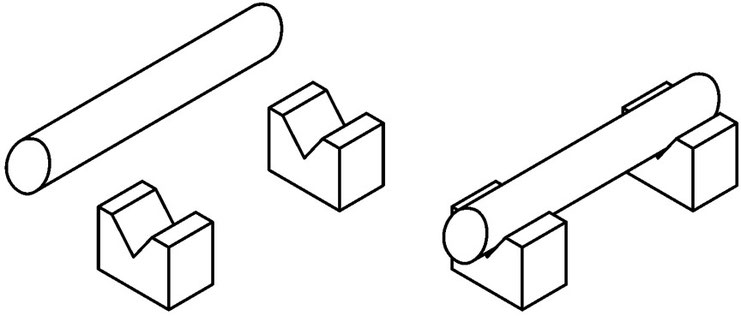
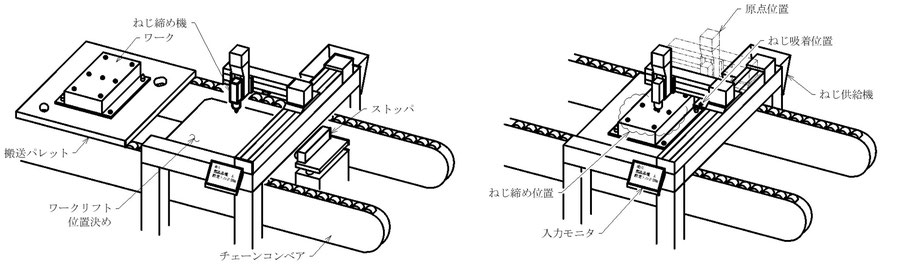
ワークが専用の搬送パレット上に固定されてチェーンコンベア上を流れてきます。
所定の位置に来たらワークを位置決め固定して、ねじ締めが開始します。
このとき、搬送パレットを自分たちで設計するのであればV字溝と丸形状で任意の位置に位置決め基準を取ることができます。
ではここで図4を見てください。
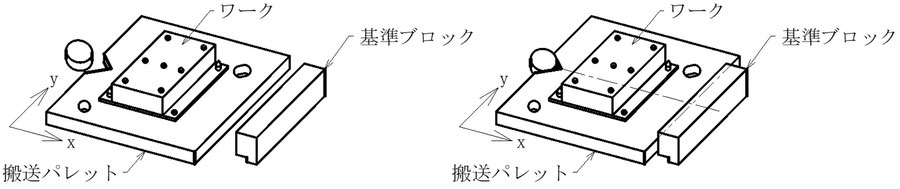
搬送パレットにV溝の切れ込みを入れます。
基準ブロックに向かって、丸いものをV溝に向かって押し付けます。
x方向は基準ブロック、y方向をV溝の位置で決めることができます。
ここで、押さえておくべきポイントは図5に示す3点の関係性です。
1ワーク加工基準
2ワークとパレットの位置決め基準
3パレットと装置の位置決め基準
この3つの関係性が悪いと自動機が作業を失敗するのは位置決め要素その1と同じです。
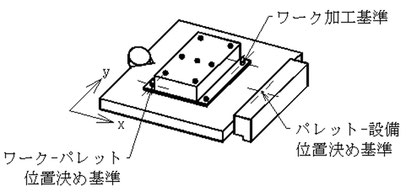
失敗しない自動機のためには
(位置決め誤差+加工誤差+機械誤差)<(その作業で許される誤差、許容誤差)
が成り立つ必要があります。成り立たない場合は次のような改善が必要になります。
(1)基準を全て合わせる。(位置決め誤差を小さくする。)
(2)各寸法誤差を見直す。(加工誤差を小さくする。)
(3)機械の精度を上げる。(機械誤差を小さくする。)
(4)設計寸法を変更する。(許容誤差を大きくする。)
(5)画像認識を利用する。(位置決め、加工誤差を無視する。)
(1)基準を全て合わせる。(位置決め誤差を小さくする。)
最も確実な手段は1.基準を全て合わせることです。例えば図6のように装置側に設けたピンでパレットとワークを一緒に決めてしまう方法などがあります。
その場合もピンと穴のクリアランス分のガタが出ますし他の理由も合わせて許容誤差を達成できない場合、あるいは基準を合わせることが不可能な場合は2.以降の方法を検討する必要があります。
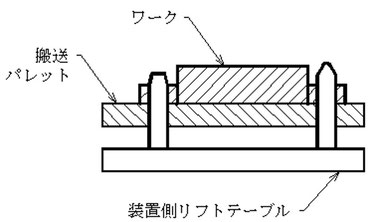
(2)各寸法を見直す。(加工誤差を小さくする。)
ワークとパレットの位置決めについては位置決め要素その3で解説します。ここではワークの加工基準とパレットの位置決め基準が同じとして、パレットを設備に固定する位置決めについて話を進めます。
パレットを設備に固定する方法は図7の通りでローラフォロア等の丸物をV溝に押し当てて固定・位置決めを行います。このとき、図8のようにパレットの加工基準が左下に取られていたらどうでしょうか。V溝と位置決めピン用のタップ、そして基準ブロックに押し当てる右側側面の関係性はありません。これでは誤差を制御して狙いの範囲に収めることはできません。図8の例で、180が+マックスの180.5、210が-ミニマムの209.5で出来た場合、ピンと端面の差は29㎜になります。逆の場合31㎜になります。つまりピンと端面の位置関係は30±1mmと大きな誤差が出ます。
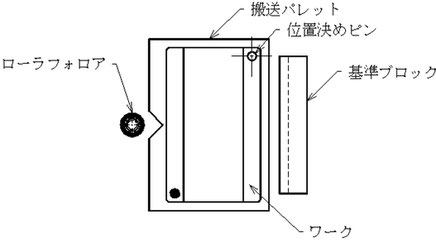
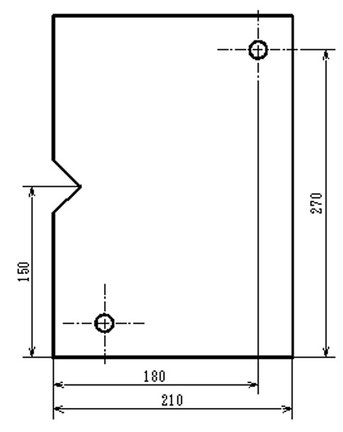
図9のように基準の取り方を変えて寸法の入れ方を変えると、30±0.2㎜となり、誤差を小さくすることができます。しかしこれではまだV溝の位置が他の基準面と関連づけられていません。このためV溝とピンの位置関係にも図8で見たように予想外の大きな誤差が生じる可能性があります。これもいくつかやり方がありますが、例えば図10のようにピン位置を基準にしてしまう方法があります。
まず、左下を基準にピン位置を出してもらい、そこから必要な加工寸法を追ってもらう方法です。ただしこの方法は、はっきり言って加工屋さんからすればあまり好ましいモノではありませんし寸法確認も手間ですので、多用せずにここぞという時に使うようにします。
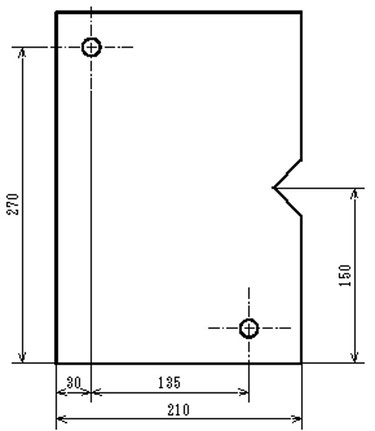
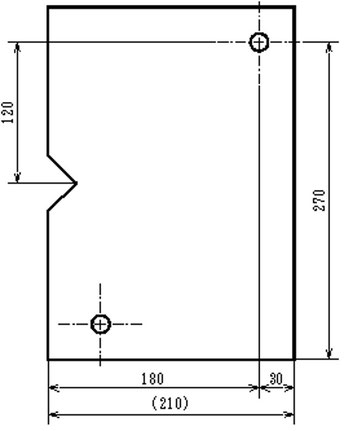
(3)機械の精度を上げる。(機械誤差を小さくする。)
協働ロボットの繰り返しの位置決め精度は、スペックによりますが10μ程度~100μ程度あります。可能ならば機械を再選定することで許容誤差内に納めることができます。
(4)設計寸法を変更する。(許容誤差を大きくする。)
作業内容によりますが、例えば丸穴にピンを挿入する作業の場合、丸穴を大きくすれば許容される誤差は大きくなります。
(5)画像認識を利用する。(位置決め、加工誤差を無視する。)
いくら位置決めがずれようが、対象の位置をカメラで認識して座標のズレを補正してしまえば、位置決めと加工の誤差は関係なくなります。
ただし、画像認識そのものの誤差があるので注意が必要です。画像認識の誤差については別途解説予定です。
前のブログは生産技術のお仕事です。
次のブログは位置決めその3です。
関連ブログは位置決め要素その1はコチラから→【位置決め要素その1】
技術資料一覧はこちらから⇒「技術資料」
コメントをお書きください